Business thrives on efficiency. And at the heart of operational efficiency lies impeccable stock management. It’s not just about knowing what you have; it's about knowing when you need it, where it is, and how to optimize its flow to fuel production. Get it right, and you'll see reduced costs, faster lead times, and happier customers. Get it wrong, and you risk bottlenecks, stockouts, and wasted resources. In this blog post, I'll walk you through the essential principles and practices of stock management, providing actionable strategies and insights to elevate your operations.

Image source: hotwaxsystems.com
Why stock management is critical for business success
Today, the ability to respond quickly to market demands is paramount, which hinges significantly on how effectively you manage your raw materials, work-in-progress (WIP), and finished goods – your stock. Efficient stock management isn’t just a “nice-to-have"; it’s a core component of business excellence and a direct contributor to your bottom line.
Imagine a scenario where a crucial component is out of stock, halting production and delaying customer orders. Or conversely, picture a warehouse overflowing with excess inventory, tying up valuable capital and incurring storage costs. Both situations highlight the critical need for a robust and well-defined stock management strategy.
Poor stock management can lead to a cascade of negative consequences, including:
Increased costs: Holding excessive inventory incurs storage costs, insurance, and the risk of obsolescence.
Production delays: Stockouts can halt production lines, leading to missed deadlines and dissatisfied customers.
Reduced profitability: Inefficient inventory practices can erode profit margins through waste, spoilage, and unnecessary expenses.
Lowered customer satisfaction: Delays and stockouts can damage your reputation and lead to lost sales.
Conversely, effective stock management unlocks a wealth of benefits:
Reduced costs: Optimizing inventory levels minimizes storage costs, waste, and obsolescence.
Improved production efficiency: Ensuring the right materials are available at the right time streamlines production processes and reduces downtime.
Enhanced profitability: By reducing costs and improving efficiency, effective inventory management directly contributes to higher profit margins.
Increased customer satisfaction: Meeting customer orders on time and in full builds trust and loyalty.
To better understand the advantages associated with stock management, I invite you to examine the following template. This framework is crafted to promote both convenience and efficiency within your stock management processes.
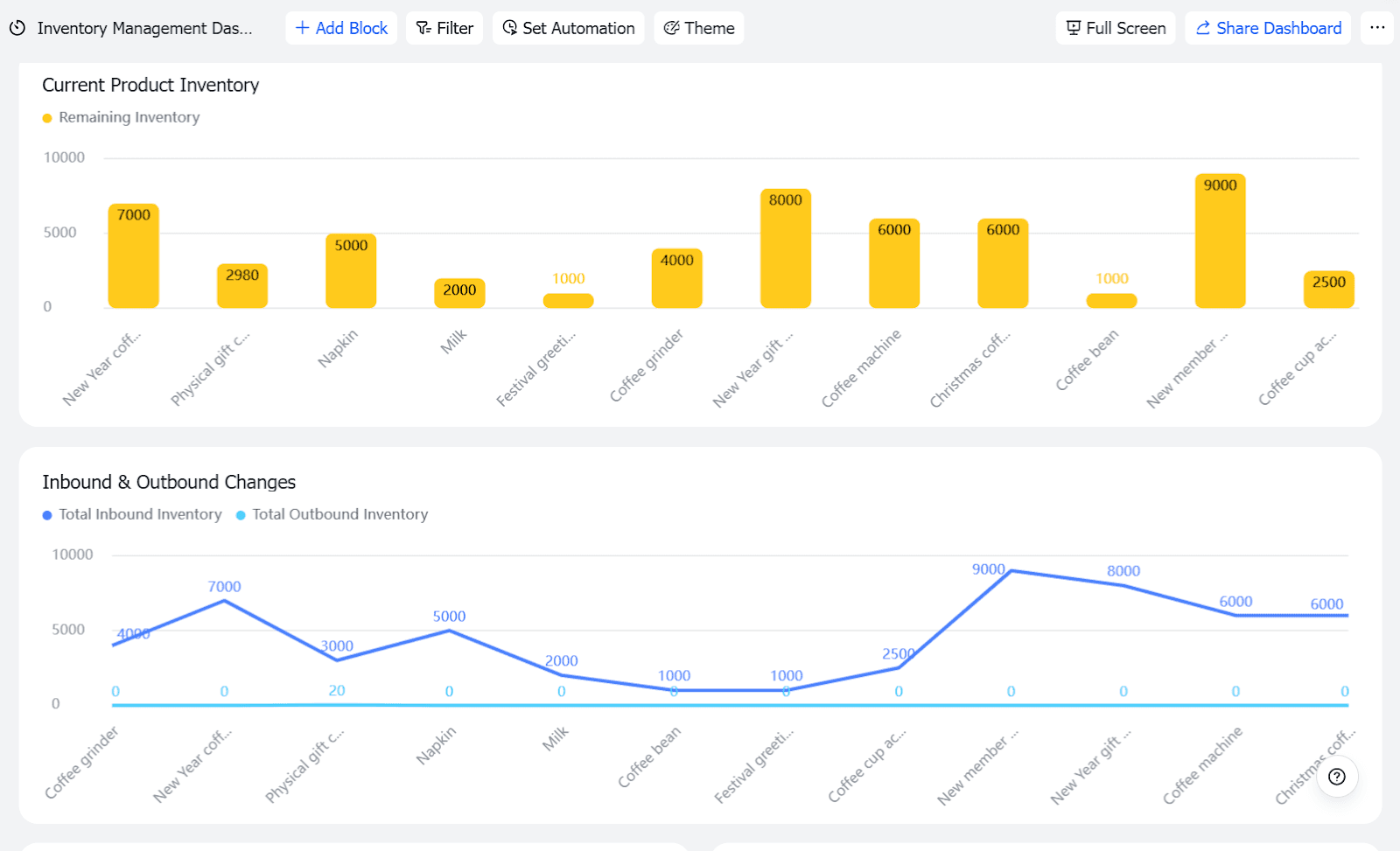
Understanding stock management essentials
At its core, stock management, also known as inventory management, is the process of planning, controlling, and optimizing the flow of goods from procurement to delivery. It encompasses all activities related to managing your inventory, including:
Inventory planning: Forecasting demand, determining optimal stock levels, and establishing replenishment strategies.
Procurement: Sourcing materials, negotiating with suppliers, and placing orders.
Receiving and storage: Receiving incoming goods, inspecting for quality, and storing them in a designated location.
Inventory control: Tracking inventory levels, monitoring stock movements, and identifying discrepancies.
Order fulfillment: Picking, packing, and shipping orders to customers.
Inventory analysis: Evaluating inventory performance, identifying areas for improvement, and making data-driven decisions.
To effectively manage these activities, it's essential to understand different types of inventory:
Raw materials: The basic inputs used in the manufacturing process (e.g., metals, plastics, chemicals). Effective management of raw materials ensures uninterrupted production and prevents costly delays.
Work-in-progress (WIP): Partially completed goods that are in the process of being manufactured. Controlling WIP levels is crucial for minimizing lead times and maximizing throughput.
Finished goods: Completed products that are ready for sale. Managing finished goods inventory involves balancing the need to meet customer demand with the desire to minimize storage costs.
Maintenance, repair, and operations (MRO) inventory: Items used to maintain and repair equipment and facilities (e.g., spare parts, lubricants, cleaning supplies). Properly managing MRO inventory ensures that equipment downtime is minimized.
Beyond the types of inventory, several key metrics are used to evaluate stock management performance. These metrics provide insights into inventory efficiency and effectiveness:
Inventory turnover ratio: Measures how quickly inventory is sold and replaced over a given period. A higher turnover ratio indicates efficient inventory management.
Formula: Cost of Goods Sold / Average Inventory
Days sales of inventory (DSI): Indicates the average number of days it takes to sell inventory. A lower DSI suggests efficient inventory management.
Formula: (Average Inventory / Cost of Goods Sold) * 365
Fill rate: Measures the percentage of customer orders that can be fulfilled immediately from available inventory. A higher fill rate indicates better customer service and fewer lost sales.
Formula: (Number of Orders Fulfilled / Total Number of Orders) * 100
Stockout rate: Measures the frequency of stockouts, or instances when inventory is unavailable to meet customer demand. A lower stockout rate indicates better inventory planning and control.
Formula: (Number of Stockout Occurrences / Total Number of Order Attempts) * 100
Holding costs: The costs associated with storing and maintaining inventory, including storage space, insurance, and obsolescence. Minimizing holding costs is a key objective of effective inventory management.
Understanding these fundamental concepts and metrics is the first step towards implementing a successful stock management strategy. In the next section, we'll explore practical techniques for optimizing your inventory and improving your bottom line.
Essential stock management techniques: A practical guide to optimization
Now that we’ve covered the foundational concepts, let’s explore some essential stock management techniques that you can implement to optimize your inventory and improve your manufacturing operations. These techniques are proven to help reduce costs, improve efficiency, and enhance customer satisfaction.
ABC analysis
The ABC analysis categorizes inventory items based on their value and consumption rate. "A" items are high-value items that require close monitoring and control, "B" items are medium-value items that require moderate attention, and "C" items are low-value items that require minimal control. By focusing your efforts on managing "A" items effectively, you can achieve significant improvements in inventory performance. For example, you might implement tighter security measures for "A" items or negotiate more favorable terms with suppliers.
Economic order quantity (EOQ)
EOQ is a mathematical model used to determine the optimal order quantity that minimizes total inventory costs, including ordering costs and holding costs. By calculating the EOQ for each inventory item, you can avoid ordering too much or too little, optimizing your inventory levels and reducing costs. The EOQ formula takes into account factors such as demand, ordering costs, and holding costs.
Just-in-time (JIT) inventory
JIT is an inventory management strategy that aims to minimize inventory levels by receiving materials only when they are needed for production. This approach requires close coordination with suppliers and efficient production processes. While JIT can significantly reduce inventory costs, it also requires careful planning and execution to avoid stockouts.
Safety stock
Safety stock is extra inventory held to buffer against unexpected demand fluctuations or supply disruptions. Determining the appropriate level of safety stock is crucial for avoiding stockouts and ensuring customer satisfaction. Factors to consider when calculating safety stock include demand variability, lead time variability, and the desired service level.
Demand forecasting
Accurate demand forecasting is essential for effective stock management. By forecasting future demand, you can plan your inventory levels accordingly, avoiding both stockouts and excess inventory. Various forecasting techniques can be used, including historical data analysis, statistical modeling, and market research.
Cycle counting
Cycle counting is a continuous inventory auditing process that involves counting a small subset of inventory items on a regular basis. This approach helps to identify and correct inventory discrepancies, ensuring accurate inventory records. Cycle counting is more efficient than a full physical inventory count, which can be time-consuming and disruptive to operations.
Vendor-managed inventory (VMI)
VMI is a supply chain management strategy in which the supplier is responsible for managing the inventory levels at the customer's location. This approach can improve inventory availability, reduce costs, and streamline the supply chain. VMI requires close collaboration and information sharing between the supplier and the customer.
Lean inventory management
Lean principles can be applied to stock management to eliminate waste and improve efficiency. This involves identifying and eliminating activities that do not add value, such as excessive inventory, unnecessary movement, and defects. Lean inventory management focuses on streamlining processes, reducing lead times, and improving quality.
Implementing these stock management techniques can significantly improve your manufacturing operations.
Power up: Leveraging technology for superior stock management
Nowadays, relying solely on manual stock management processes is akin to navigating with an outdated map. Let's explore the key technologies that are revolutionizing how we manage stock.
Enterprise resource planning (ERP) systems
Think of ERP systems as the central nervous system of your manufacturing operations. They integrate various business functions, including stock management, production planning, order management, and finance, into a unified platform. By providing a real-time view of your inventory levels, demand forecasts, and supply chain activities, ERP systems empower you to make data-driven decisions. You can anticipate potential shortages, optimize order quantities, and minimize carrying costs.
Warehouse management systems (WMS)
While ERP systems provide a broad overview of your operations, WMS solutions focus specifically on optimizing warehouse operations. They streamline everything from receiving and putaway to picking, packing, and shipping. By automating tasks, optimizing workflows, and improving space utilization, WMS solutions can significantly boost warehouse efficiency and accuracy.
Barcode and RFID technology
These technologies provide a powerful way to track inventory items in real-time. Barcode scanners allow you to quickly and accurately identify and track products as they move through the supply chain. Radio Frequency Identification (RFID) technology takes it a step further by enabling you to track items wirelessly and from a distance. This is particularly useful for managing high-value or time-sensitive inventory.
Advanced planning and scheduling (APS) systems
APS systems help you optimize production schedules based on real-time demand, capacity, and material availability. By considering all relevant constraints, APS systems can generate optimal production plans that minimize lead times, reduce bottlenecks, and improve on-time delivery performance.
AI and machine learning
These emerging technologies are poised to revolutionize stock management even further. AI-powered forecasting algorithms can analyze vast amounts of data to predict demand with unprecedented accuracy. Machine learning can also be used to optimize inventory levels, identify potential supply chain disruptions, and automate various stock management tasks.
Common stock management challenges and how to overcome them
Even with the most sophisticated systems in place, stock management isn't always smooth sailing. Unexpected challenges can arise, disrupting operations and impacting profitability. Let's delve into some of the most common challenges and strategies for tackling them head-on.
Inaccurate demand forecasting
One of the biggest challenges is predicting future demand accurately. Overestimating demand can lead to excess inventory and storage costs, while underestimating demand can result in stockouts and lost sales.
Solution: Invest in robust demand forecasting tools and techniques. Utilize historical data, market trends, and sales forecasts to develop accurate demand plans. Regularly review and adjust your forecasts based on real-time data and feedback from sales and marketing teams. Consider using statistical forecasting methods or AI-powered forecasting tools for more accurate predictions.
Inventory shrinkage
Shrinkage, which refers to the loss of inventory due to theft, damage, or obsolescence, can significantly impact your bottom line.
Solution: Implement robust security measures to prevent theft. Invest in proper storage and handling procedures to minimize damage. Regularly review your inventory to identify and dispose of obsolete or slow-moving items. Consider using cycle counting to verify inventory accuracy and identify discrepancies.
Supply chain disruptions
Unexpected events, such as natural disasters, geopolitical instability, or supplier bankruptcies, can disrupt your supply chain and lead to stockouts.
Solution: Diversify your supplier base to reduce reliance on a single source. Develop contingency plans to address potential supply chain disruptions. Invest in supply chain visibility tools to track shipments and identify potential delays. Consider holding safety stock to buffer against unexpected disruptions.
Inefficient warehouse operations
Inefficient warehouse layouts, processes, and equipment can lead to delays, errors, and increased costs.
Solution: Optimize your warehouse layout to minimize travel distances and improve workflow. Implement efficient picking and packing processes. Invest in warehouse automation technologies, such as conveyor systems, automated guided vehicles (AGVs), and automated storage and retrieval systems (AS/RS).
Lack of real-time visibility
Without real-time visibility into inventory levels, demand, and supply chain activities, it's difficult to make informed decisions and respond quickly to changing conditions.
Solution: Implement a comprehensive inventory management system that provides real-time visibility into your inventory levels across all locations. Integrate your inventory management system with other business systems, such as your ERP, WMS, and CRM systems. Use mobile devices and barcode scanners to track inventory movements in real-time.
Learn more 👉Inventory Management Software for Small Business: Best tools in 2025
How Lark can revolutionize your stock management
I’ve talked a lot about stock management, and it’s important to connect these ideas to solutions. Lark, an all-in-one platform, can genuinely transform your approach to stock management, leading to improved efficiency, collaboration, and ultimately, greater profitability.

Real-time data and analytics
Lark Base integrates with various data sources, providing real-time insights into your inventory levels, sales data, and supply chain performance. You can use Lark Dashboards to visualize key metrics and identify trends, allowing you to make data-driven decisions. This helps you optimize stock levels, reduce waste, and improve forecasting accuracy.

Centralized information hub
Lark provides a central hub for all your stock management information, eliminating silos and ensuring that everyone is on the same page. With Lark Docs, you can create and share inventory lists, standard operating procedures (SOPs), and training materials. This ensures consistency and reduces the risk of errors. Furthermore, with its powerful search capabilities, information is always readily accessible, saving valuable time and effort.

Streamlined communication and collaboration
Effective communication is crucial for successful stock management. Lark Messenger facilitates real-time communication between team members, suppliers, and customers. You can create dedicated channels for specific projects or tasks, ensuring that everyone is kept informed of progress and any potential issues. This eliminates the need for endless email chains and improves responsiveness.
Automated workflows and approvals

Lark Approval's automation features can streamline various stock management processes, such as purchase order approvals, inventory updates, and reorder points. You can create custom workflows that trigger automatically based on predefined rules. This reduces manual effort, minimizes errors, and speeds up the entire process. For instance, you can set up a workflow that automatically generates a purchase order when inventory levels fall below a certain threshold.
Mobile accessibility
With Lark's mobile app, you can access all your stock management information and communication tools from anywhere, at any time. This is particularly useful for field staff who need to check inventory levels, process orders, or communicate with colleagues on the go. Mobile accessibility improves responsiveness and ensures that you are always connected to your business.
By leveraging Lark's powerful features, you can transform your stock management processes, improve collaboration, and drive greater efficiency. Lark can act as a catalyst for operational excellence.
FAQs
What is the difference between stock management and inventory management?
While often used interchangeably, stock management typically refers to the control of goods within a warehouse or storage facility, whereas inventory management encompasses a broader scope, including the entire supply chain, from procurement to distribution. Think of stock management as a component within the broader field of inventory management. The management of stock may be part of the broader inventory management.
How do I determine the optimal stock level for my business?
Determining the optimal stock level requires careful analysis of several factors, including demand forecasting, lead times, carrying costs, and stockout costs. You should strive to balance the need to meet customer demand with the desire to minimize inventory holding costs. Techniques like Economic Order Quantity (EOQ) and safety stock calculations can be helpful. In reality, there is no magic formula.
What are some effective ways to reduce inventory holding costs?
Several strategies can help reduce inventory holding costs, including optimizing order quantities, improving demand forecasting accuracy, implementing just-in-time (JIT) inventory management, and negotiating better terms with suppliers. Also, don't forget the low-hanging fruit: ensure your warehousing is organized and efficient!
How can I improve communication with my suppliers?
Clear and consistent communication with suppliers is essential for effective stock management. Use tools such as Lark Messenger to facilitate real-time communication, share forecasts, and track orders. Building strong relationships with your suppliers can also lead to better terms and improved responsiveness. A collaborative relationship is key.
What are some common stock management mistakes to avoid?
Common stock management mistakes include poor demand forecasting, inadequate safety stock levels, inefficient warehousing practices, and lack of communication with suppliers. Avoiding these mistakes can significantly improve your stock management performance. Don't underestimate the value of regular audits!
Conclusions
Effective stock management is no longer just a back-office function; it’s a strategic imperative for manufacturing excellence. By understanding the fundamentals, embracing new technologies, and adopting best practices, you can optimize your inventory levels, reduce costs, and improve customer satisfaction. The journey to optimized stock management is an ongoing process of continuous improvement, adaptation, and innovation.
The future of stock management is bright, with advancements in AI, automation, and data analytics paving the way for even greater efficiency and resilience. Embrace these changes, invest in the right tools, and empower your team to drive sustainable improvements. With the right strategy and the right tools, you can transform your stock management processes and achieve manufacturing excellence. Consider leveraging platforms like Lark to streamline your operations and foster a more collaborative and efficient work environment, boosting productivity and profitability.
Table of Contents